Understanding Downhole Filters: Enhancing Efficiency in Drilling Operations
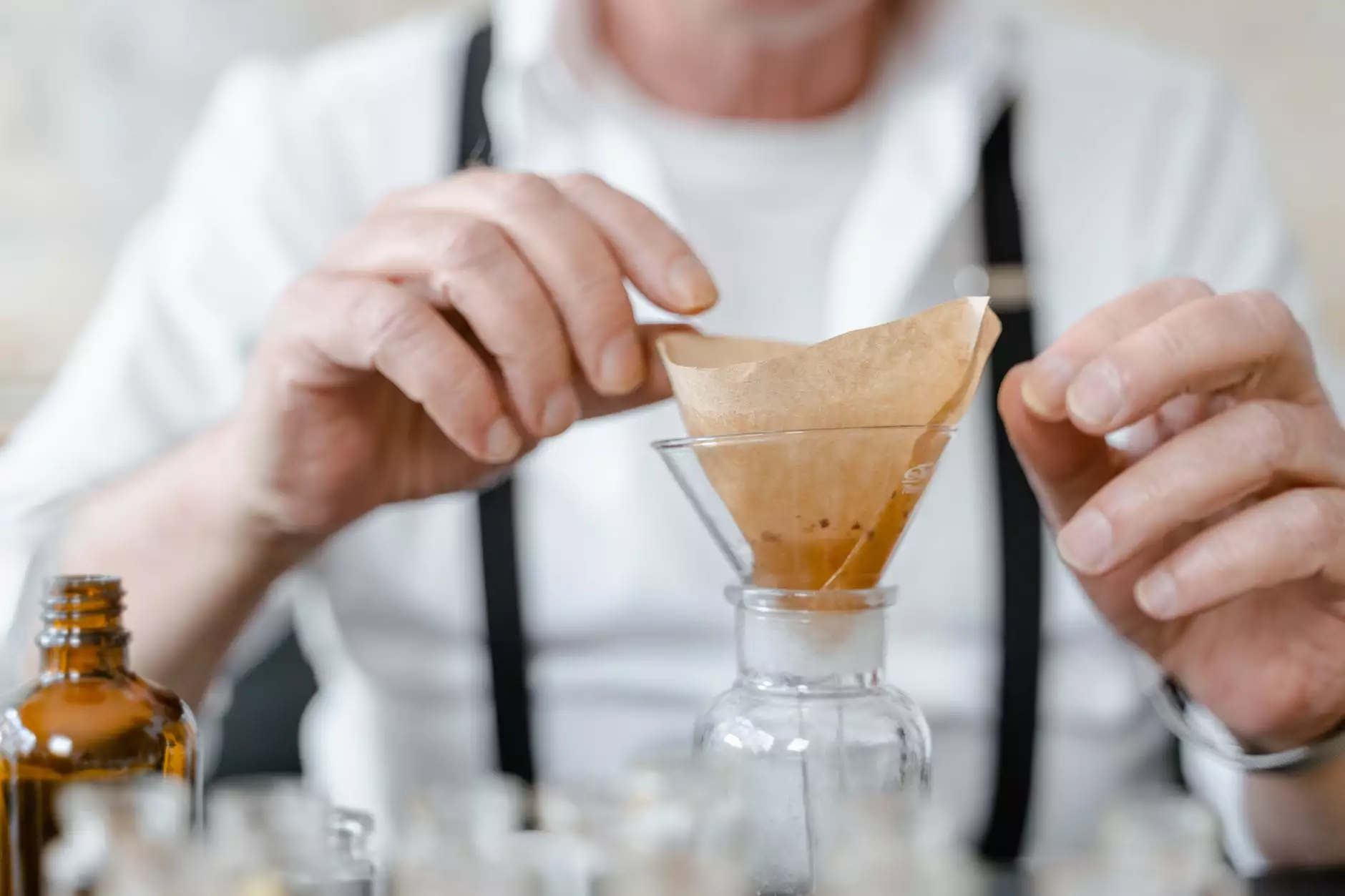
Downhole filters play a crucial role in the drilling industry, especially in the context of building supplies and machine & tool rental. As projects demand higher efficiency and lower operational costs, these filtering systems have emerged as essential components in drilling applications. This article will delve into the importance, functionality, and benefits of downhole filters, elucidating their pivotal role in modern drilling operations.
The Role of Downhole Filters in Drilling Applications
In the dynamic field of drilling, downhole filters serve to protect equipment and optimize performance. They are specifically designed to remove particulate matter and contaminants from drilling fluids, ensuring a smooth and efficient drilling process. Below are key functions of downhole filters in drilling applications:
- Contamination Control: They effectively filter out solids and other contaminants that can cause damage or interference to drilling equipment.
- Fluid Clarification: By maintaining fluid cleanliness, downhole filters enhance the overall performance of drilling fluids, contributing to better drilling efficiency.
- Extended Equipment Life: With contaminants filtered out, the longevity of drilling machinery is significantly improved, reducing maintenance costs and downtime.
- Improved Drilling Rates: Clean drilling fluids allow for faster penetration rates, thus improving overall productivity in drilling operations.
Types of Downhole Filters
There are various types of downhole filters, each tailored for specific applications and environments in drilling. Understanding the different types is essential for optimal selection based on the project’s requirements:
1. Wire Mesh Filters
Wire mesh filters consist of woven wire strands that create a mesh capable of capturing larger particles. These are often reusable and can be cleaned easily, making them a cost-effective option for many projects.
2. Cartridge Filters
Cartridge filters are designed for finer filtration needs. They typically contain filter media that captures smaller particulates, thus ensuring high fluid purity during drilling operations.
3. Screen Filters
Screen filters provide a physical barrier to block debris while allowing fluids to pass through. They are particularly useful in environments with substantial solid content in the drilling fluid.
4. Hydrocyclone Filters
Hydrocyclone filters leverage centrifugal force to separate particles from drilling fluids. They are effective in removing sand and larger particles, making them a popular choice in high-solids environments.
Benefits of Implementing Downhole Filters
The integration of downhole filters into drilling operations presents numerous benefits that not only enhance efficiency but also drive sustainability in the drilling sector. Here are some pivotal advantages:
- Cost Savings: By reducing wear and tear on equipment and minimizing downtime, businesses can significantly lower operational costs associated with drilling.
- Enhanced Safety: Clean drilling fluids minimize the risk of equipment failure and blowouts, leading to a safer working environment for personnel.
- Sustainability: Proper filtration enables the reuse of drilling fluids, reducing waste and environmental impact of drilling activities.
- Regulatory Compliance: Effective filtration helps companies meet environmental regulations by ensuring that discharged fluids are free from harmful contaminants.
Choosing the Right Downhole Filter for Your Project
Selecting the appropriate downhole filter entails understanding the specific requirements of your drilling project. Consider the following factors:
- Particle Size: Determine the size of the particulates you need to filter out. This will influence your choice of filter type.
- Fluid Type: The nature of the drilling fluid (water-based, oil-based, synthetic) can affect filter performance.
- Flow Rate: Assessing the required flow rate is crucial to ensure that the filter does not restrict operations.
- Environmental Conditions: Understand the specific conditions of the drilling site, including temperature, pressure, and presence of corrosive materials.
Innovations in Downhole Filter Technology
The field of downhole filtration is constantly evolving, and new technologies are emerging to enhance the efficiency and effectiveness of these systems. Below are some notable innovations:
1. Self-Cleaning Filters
Self-cleaning filters use advanced mechanisms to remove debris from the filtration surface, reducing downtime and maintenance efforts. This technology is particularly valuable in high-flow applications where continuous operation is paramount.
2. Smart Filtration Systems
With the rise of IoT and data analytics, smart filtration systems are now capable of monitoring filter performance in real-time. These systems can provide insights into when maintenance is needed, enhancing operational efficiency.
3. Nano-Filtration Technologies
Emerging nano-filtration technologies aim to improve the capture of ultra-fine particles, enabling even cleaner drilling fluids and contributing to better overall drilling performance.
Implementing Downhole Filters in Your Operations
Integrating downhole filters into your drilling operation requires careful planning and implementation. Here are steps to consider:
- Assessment: Conduct a thorough assessment of your current drilling operation's filtration capabilities.
- Selection: Choose filters that align with the specific needs of your drilling activities.
- Training: Ensure that your personnel are properly trained on the installation and maintenance of downhole filters.
- Monitoring: Establish a system for monitoring filter performance to ensure optimal operation.
Conclusion
In summary, downhole filters are a fundamental component of efficient drilling operations. Their ability to protect equipment, reduce costs, and enhance safety makes them indispensable in the construction and rental industry. As technology advances, the effectiveness and adaptability of these filters will continue to improve, solidifying their role in the future of drilling. Investing in quality downhole filters is an investment in the long-term success and sustainability of drilling projects, positioning companies at the forefront of operational excellence.
Contact Maverick Drilling for Your Downhole Filter Needs
If you are looking to implement effective downhole filters in your drilling projects, Maverick Drilling is your go-to resource for top-quality equipment and expert advice in building supplies and machine & tool rentals. Our extensive knowledge and commitment to client satisfaction set us apart in the industry, ensuring that your operations are efficient and successful. Contact us today to discuss how we can support your drilling needs!