Understanding LOLER: Definition and Importance for Businesses
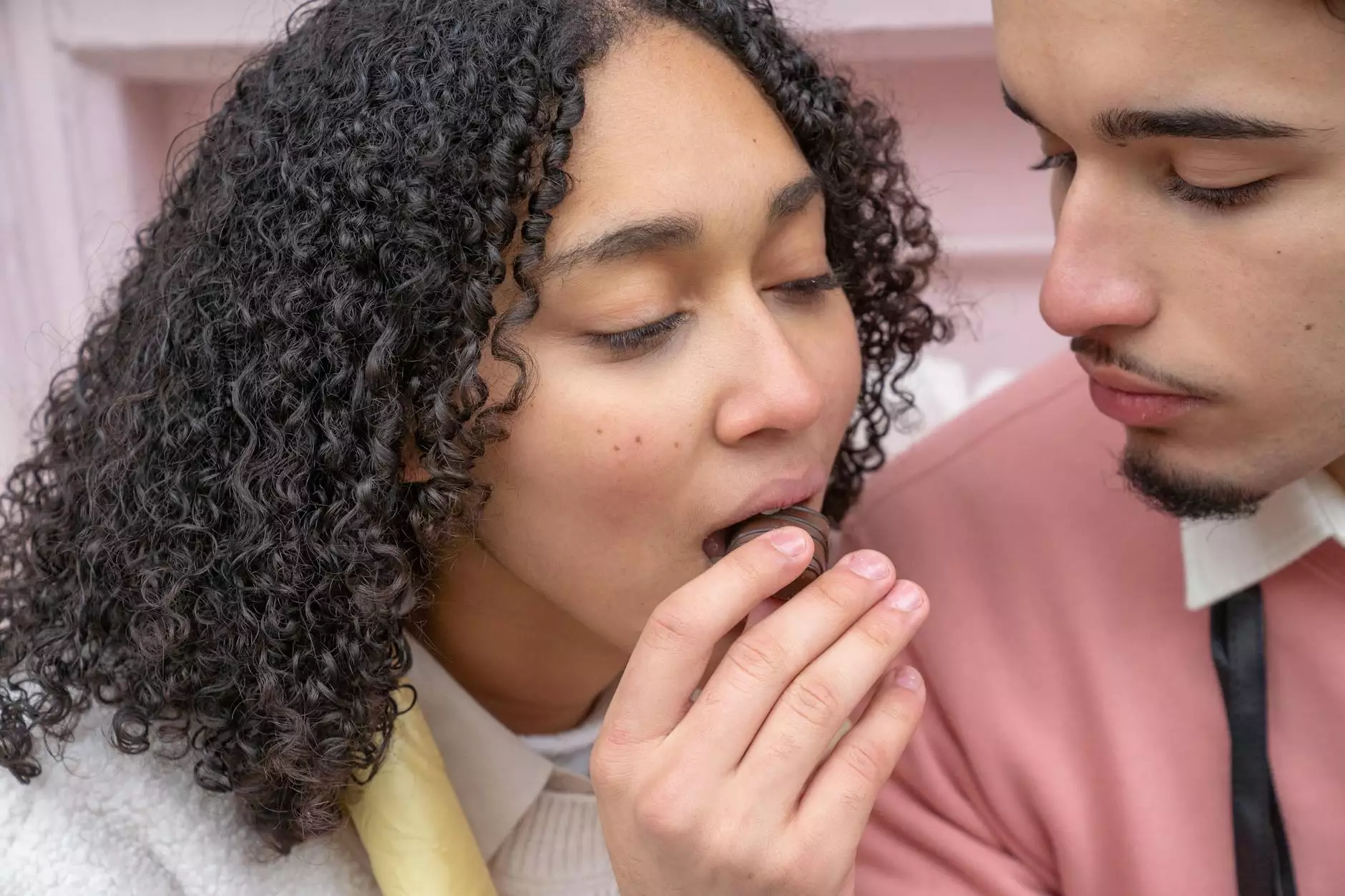
In today’s rapidly evolving business environment, understanding regulations is crucial for success. One such important regulation is LOLER, which stands for Lifting Operations and Lifting Equipment Regulations. This legislation plays a pivotal role in ensuring safety standards in various industries, including Home & Garden, Gardeners, and Pest Control. In this article, we will delve into the LOLER definition, its implications for businesses, and why compliance is fundamental.
What is LOLER?
The LOLER legislation was established in the UK to ensure that lifting operations are carried out safely. It applies to all businesses and organizations that use lifting equipment, which includes everything from cranes to more specialized equipment used by gardeners and pest control professionals.
Understanding the LOLER definition is essential for anyone involved in managing lifting operations. It focuses on the equipment used for lifting and the conditions under which those lifts are performed. The regulation mandates that:
- All lifting equipment must be suitable for the intended use.
- Equipment must be properly maintained and regularly inspected.
- Operators must be adequately trained and experienced.
- Risks must be assessed before any lifting operation.
The Importance of LOLER Compliance
Compliance with LOLER is not just a legal obligation; it is vital for ensuring the safety of employees and protecting the business from legal liabilities. Here are several key reasons why adherence to this regulation is crucial:
1. Enhancing Workplace Safety
By following LOLER requirements, companies can significantly reduce the risk of accidents and injuries associated with lifting operations. For example, in the Pest Control industry, when using lifting equipment to access treatment areas, ensuring that this equipment is safe and well-maintained is critical.
2. Legal Protection
Non-compliance with LOLER can lead to severe legal consequences, including fines, legal action, and even imprisonment for gross negligence. By adhering to LOLER regulations, businesses safeguard themselves against such risks.
3. Financial Savings
While some may view compliance as an additional cost, the reality is that it can save money in the long run. Accidents caused by improper lifting practices can be costly, not only in terms of financial loss but also due to damage to reputation and loss of business.
4. Improved Business Reputation
Being known as a safe and compliant business enhances your reputation among customers and partners. This reputation is crucial for businesses in the Home & Garden industry, where safety concerns can influence purchasing decisions.
Key Components of LOLER
To fully grasp the LOLER definition and its implications, it is important to understand its key components:
A. Suitable Equipment
LOLER mandates that lifting equipment must be suitable for the intended lifting operations. This includes considerations of the load's weight and the height of the lift. Equipment that is too small or unfit for purpose poses significant risks.
B. Regular Inspections
Regular inspections are fundamental under LOLER. Equipment must be examined every six months, and records of these inspections should be maintained. This ensures any potential issues are identified and addressed promptly.
C. Operator Training
Operators must receive appropriate training to safely use lifting equipment. This includes understanding how to assess loads, operate machinery, and respond appropriately to potential hazards.
Implementing LOLER in Your Business
For businesses in the Home & Garden, Gardeners, and Pest Control sectors, implementing LOLER can involve several steps:
1. Conduct a Risk Assessment
Evaluate the types of lifting operations you perform and identify any risks associated with your equipment and procedures. This assessment will guide your compliance efforts.
2. Choose the Right Equipment
Select equipment that is suitable for your lifting needs. Consult manufacturers and safety professionals for recommendations.
3. Establish a Maintenance Schedule
Create and adhere to a maintenance schedule for all lifting equipment. This should include regular inspections and immediate repairs for any identified issues.
4. Train Your Staff
Provide comprehensive training for all employees involved in lifting operations. Make sure they are aware of LOLER regulations and your internal safety procedures.
5. Keep Records
Maintain detailed records of inspections, maintenance, and training. This documentation is crucial for demonstrating compliance and for internal evaluations of safety practices.
The Future of LOLER and Business Compliance
As technology and methods evolve, so too do regulations. The future may see updates to LOLER to account for new lifting techniques and equipment. Businesses must stay informed and adapt their practices accordingly.
Investing in compliance not only protects employees but also enhances operational efficiency and contributes to a positive workplace culture. As the business landscape becomes increasingly competitive, those that prioritize safety and compliance will be better positioned for success.
Conclusion: The Essential Role of LOLER in Business
In conclusion, understanding the LOLER definition and its implications for your business is critical. Compliance with these regulations is not just a legal responsibility; it is a commitment to safety, efficiency, and the well-being of employees. For businesses in the Home & Garden, Gardeners, and Pest Control industries, adhering to LOLER can lead to enhanced safety practices, legal protection, and an improved reputation.
By prioritizing compliance and fostering a culture of safety, your business will not only meet legal standards but excel in providing safe and reliable services to customers. Don't underestimate the significance of LOLER – it is essential for every operational aspect in lifting scenarios across all industries.